Predictive Maintenance Program (PMP)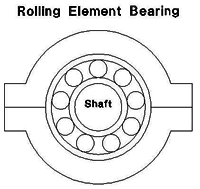 A Quality Rotating Machinery Predictive Maintenance (PM) Program for your facility will return your investment many times over. This type of PM Program is based on periodic vibration measurements of your Rotating Machinery. In many cases, a Return On Investment (ROI) of less than one year (six months typical) is quite common. A Contract PM Program eliminates the initial capital investment required to conduct your own PM Program.
There are three classifications of machinery maintenance methods: Breakdown, Preventative, and Predictive Maintenance. Each method has its own associated costs and benefits.
Breakdown Maintenance, by its own nature, is the most expensive method of plant maintenance. This method has no scheduled maintenance until a machine destroys itself, and it must be replaced at great cost. The machine breakdown often brings the production process to an immediate halt. Breakdown Maintenance has high costs in manpower, replacement parts, and lost production.
Preventative Maintenance, the next logical method, relies on a periodic inspection the machines. During the inspection, machine damage is found and corrected. This method requires a large inventory of replacement parts prior to the machine's inspection. Preventative Maintenance has a lower associated cost because manpower can be planned in advance.
Predictive Maintenance involves monitoring the machine's vibration characteristics or symptoms to diagnose its condition. This method relies on the machine's condition to accurately schedule the repair interval. The machine's condition also determines the required replacement parts. Predictive Maintenance has the lowest cost of the three methods with the highest possible savings.
A Machinery PM Program is beneficial to all industries that have rotating machinery on their site such as:
Petroleum |
Chemical |
Power Generation |
Co-Generation |
Pulp and Paper |
Water Treatment |
Building Services |
HVAC |
Mining |
Food Processing |
Typical Rotating Machinery commonly included in a Machinery PM Program include but are not limited to the following:
Electric Motors |
Pumps |
Fans |
Gear Boxes |
Turbines |
Compressors |
Paper Machines |
Reciprocating Machines |
Blowers |
Machine Tools |
Chillers |
Conveyors |
PM Program
A Rotating Machinery PM Program involves the scheduled collection of vibration data from the various machines. All rotating machinery vibrates, and this vibration will increase as the equipment wears. The periodically collected vibration data can be analyzed by a trained engineer or technician to determine the cause and the required machinery repair. An initial machine inspection is usually done to determine the machinery parts that are subject to wear.
PM Program Benefits
Quality PM Programs from many industries have shown that Rotating Machinery PM Programs will:
- Reduce Capital Investment
- Reduce Machinery Depreciation
- Reduce Machinery Breakdowns
- Increase Machinery Life
- Increase Maintenance Staff Productivity
- Reduce Dissatisfied/Lost Customers
- Reduce Penalties
- Reduce Unnecessary Machinery Repairs
- Reduce Rework
- Reduce Scrap
- Reduce Warranty Claims
- Increase Credibility and Reliability
- Reduce Overtime
- Increase Safety and Reduce Penalties
- Reduce Injuries
- Reduce Power Consumption
- Reduce Spare Parts Inventory
- Reduce Defects on New Machinery
- Reduce "Wrong" Repairs
- Reduce Insurance Costs
PM Program Survey
To see if a PM Program is beneficial to you, STI will survey your facility. STI will then help you complete a "PM Program Justification Form". This no-charge survey will include:
- Review machinery and layout.
- List all applicable machinery.
- Review current and past problems.
- Determine machinery classifications.
- Determine the number of data points.
- Determine time needed to collect data.
- Determine data collection schedule.
- Start collection of the information required to complete a Program Justification.
After all the information has been acquired to complete a "PM Program Justification Form", a complete proposal will be sent to you for approval and comment.
PM Program Implementation
A PM Program can be implemented in several ways. One of which will be suitable to your facility, current knowledge, and budget. You may chose to make a capital investment for the hardware, software, and training, or a complete Machinery PM Program may be contracted from STI. A contract PM Program reduces capital investment to zero, and permits the PM Program to start in a timely fashion. When you are ready to acquire the appropriate hardware, software, and training to proceed on your own, the complete PM Program package can be turned over to you.
Once you have determined that a contract PM Program works best for you, an STI vibration engineer or technician will return to your facility.
They will do a complete facility survey to identify machinery, locate data collection points, possibly determine bearings, and formulate the data collection route. After this information is acquired, they will complete the following off site using a state of the art PM Program Software Package:
- Program facility and machinery information into PM Software.
- Program appropriate bearing and alarm information into software.
- Establish trending and exception list reporting.
- Establish Stage 1 to Stage 4 bearing failure criteria for all machinery.
Once the survey information has been properly programmed, the STI vibration engineer or technician will schedule a return trip to your facility to do the following:
- Collect initial baseline vibration data.
- Review overall vibration data for immediate action.
- Provide a written report.
Scheduled PM Program
Once the initial survey and initial baseline information is programmed, the STI vibration engineer or technician will return on a scheduled basis. For a reliable PM Program, the normal schedule is either once or twice a month. During these visits, vibration data will be collected along with a visual inspection. After the visit, you will receive the following:
Before leaving the facility:
- Exception report showing items requiring immediate attention.
By delivered report:
- Exception report of items requiring future attention.
- Report of all machines showing categories Stage 1 to Stage 4 bearing failure.
Advantages to Contract PM Programs
There are several important advantages in contracting your initial Machinery PM Program with STI:
- Immediate Results By using a highly trained and experienced STI vibration engineer or technician, immediate results are usually apparent. After several visits, the credibility and reliability of the program will be proven.
- No Capital Investment A quality PM program requires state of the art Data Collectors, Software, Computer Hardware, and Training. No capital investment is required for a contract PM Program.
- No Training Required
All of STI's engineers and technicians have many years of experience in the field of machinery vibration. Therefore, your maintenance personnel do not require training to initiate a PM Program. If you desire, your maintenance personnel can accompany STI personnel during their surveys and learn how a PM Program works. |